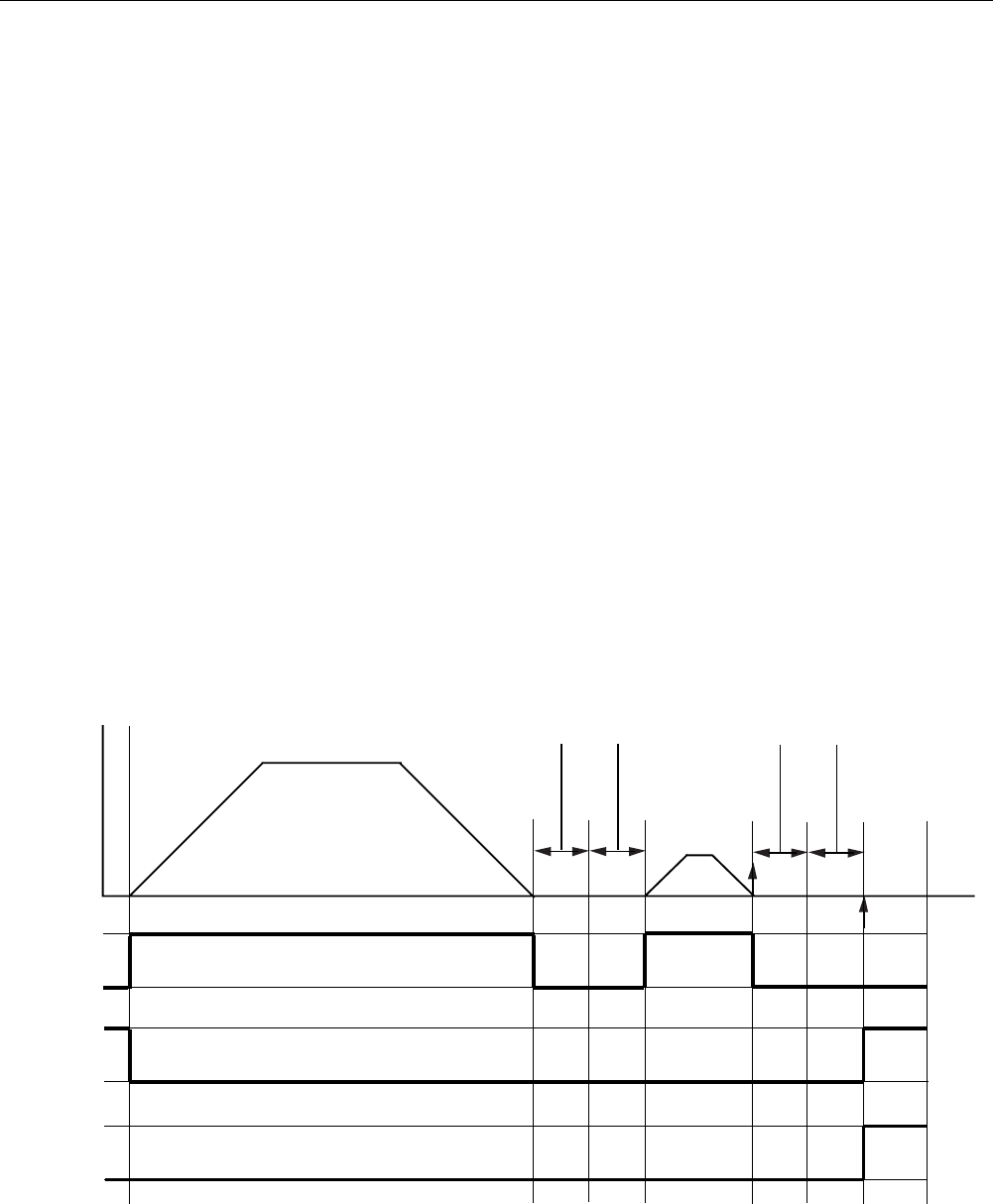
VIX IM MICROSTEPPER INDEXER DRIVE USER GUIDE
88
position using the 1R(PA) command. Now, rotate the encoder shaft in the same positive
direction by about half a turn. Again read the encoder position, which should be greater than
the first reading, indicating that the encoder count is increasing for positive motion. If the
second count is less than the first, cross over the A- and A+ signals on the encoder
connector, and repeat the test until an increasing count is obtained. Encoder signal A
should lead B for positive motion.
Note for a load mounted encoder, that is with LOADENC enabled, the system variable EM
may be set to a negative value as an alternative to crossing over A- and A+ signals on the
encoder connections.
Position Maintenance
Position Maintenance is a method of correcting occasional position errors by adding or
subtracting motor steps once a move has been completed. It is not like a servo loop in
which position error corrections are made throughout the entire move.
To be able to make use of Position Maintenance a drive system needs to be fitted with a
load or motor mounted encoder. The drive’s controller will detect the difference between the
number of steps the motor was commanded to move and the number of steps actually being
reported by the encoder. This resultant position error is used, at the end of a move, to
further command the motor in a direction to give the correct target encoder position, as
shown in Figure 4-13.
Velocity
main move
Time
Target
MV
IT
Settle
time
Position
maintenance
move
IT
Settle
time
1
1
0
0
IP
(revs/sec)
0
1
0
OUTPUT
Figure 4-13. Position Maintenance Move Profile