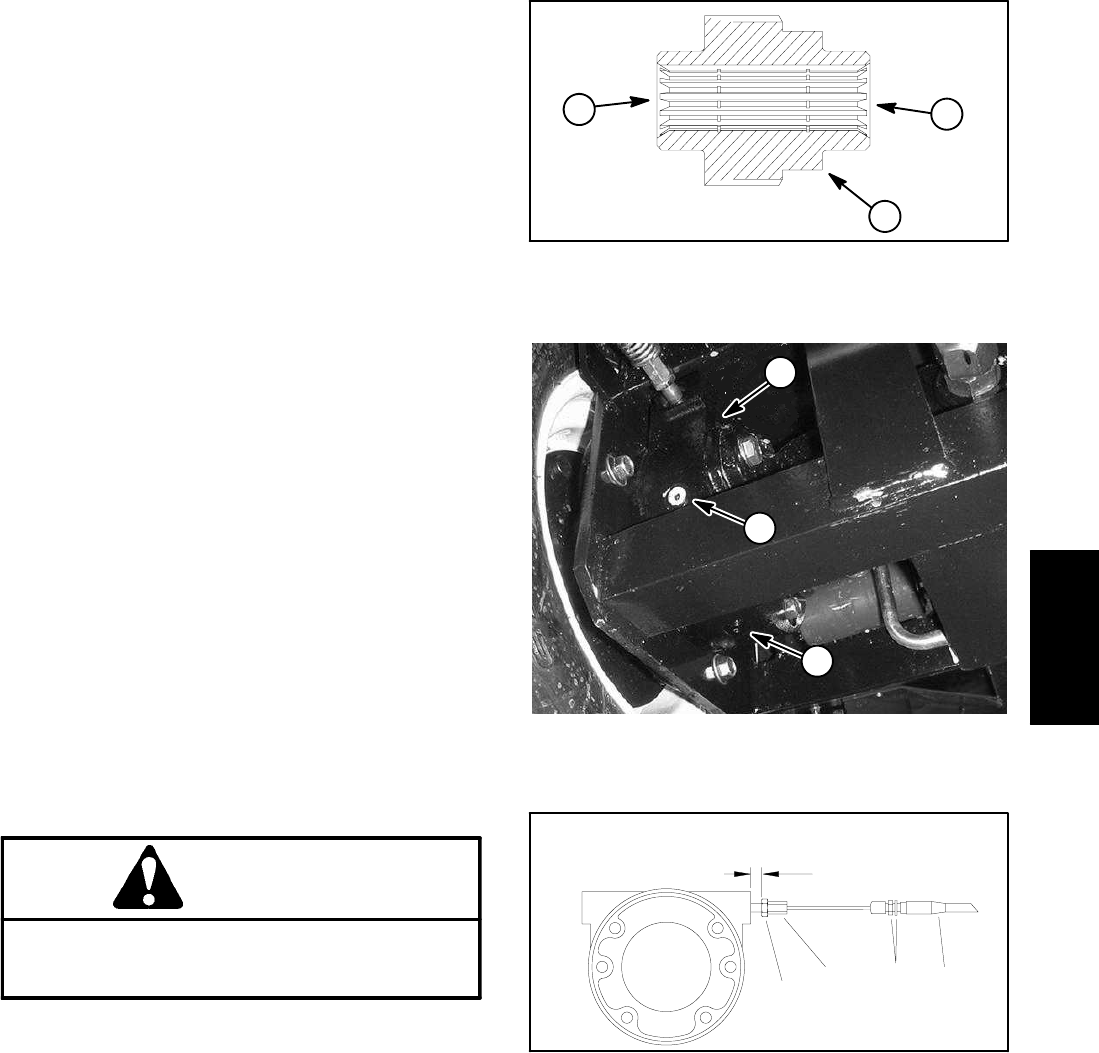
Groundsmaster 4000--D Page 6 -- 5 Axles, Planetaries and Brakes
3. Chock rear wheels and jack up front of machine (see
Jacking Instructions in Chapter 1 -- Safety). Support ma-
chine with jack stands.
4. Remove front wheel assembly.
5. Remove hydraulic wheel motor (see Front Wheel
Motors in the Service and Repairs section of Chapter 4
-- Hydraulic System).
6. Disconnect brake cable from pull rod on brake as-
sembly.
7. Support brake assembly to prevent it from falling.
8. Remove flange head cap screws (item 9) securing
brake assembly to frame.
9. Remove brake assembly from machine. Be careful
to not drop splined brake shaft as brake assembly is re-
moved.
10.Remove splined brake shaft from brake assembly.
11.Complete brake inspection and repair (see Brake In-
spection and Repair in this section).
Installation (Fig. 1)
1. Install splined brake shaft into brake assembly.
NOTE: The stepped end of the splined brake shaft must
be aligned toward the hydraulic wheel motor (Fig. 2).
2. Install brake assembly onto frame, aligning splined
brake shaft with input shaft on planetary wheel drive.
3. Secure brake assembly to frame with flange head
screws (item 9). Tighten screws in a crossing pattern to
a torque from 75 to 85 ft--lb (101 to 115 N--m).
4. Install brake cable to pull rod on brake assembly.
Brake cable end should be completely threaded onto
pull rod before tightening jam nut.
5. Install new O--ring on hydraulic wheel motor. Install
wheel motor and torque cap screws from 75 to 85 ft-- lb
(101 to 115 N--m).
WARNING
Failure to maintain proper wheel lug nut torque
could result in failure or loss of wheel and may
result in personal injury.
6. Install wheel assembly.
7. Lower machine to ground. Torque lug nuts from 85
to 100 ft--lb (115 to 135 N--m).
8. Make sure drain plug is installed in bottom of brake
assembly (Fig. 3). Fill planetary wheel drive/brake as-
sembly with SAE 85W--140 gear lube. Capacity is
approximately 16 fl. oz. (0.47 liters) per wheel.
9. Check and adjust brake cables for proper brake op-
eration. If necessary, adjust brake cable jam nuts at
frame bracket so that pull rod jam nut is positioned from
0.470” to 0.530” (12.0 to 13.4 mm) from brake casting
surface when brakes are disengaged (Fig. 4).
1. Splined brake shaft step
2. Hydraulic motor end
3. Planetary assembly end
Figure 2
1
2
3
1. Brake housing
2. Check plug
3. Drain plug
Figure 3
3
1
2
1. Pull rod jam nut
2. Brake cable end
3. Cable jam nut
4. Brake cable
Figure 4
1
2
3
4
0.470” to 0.530”
(12.0 to 13.4 mm)
Axles, Planetaries
and Brakes