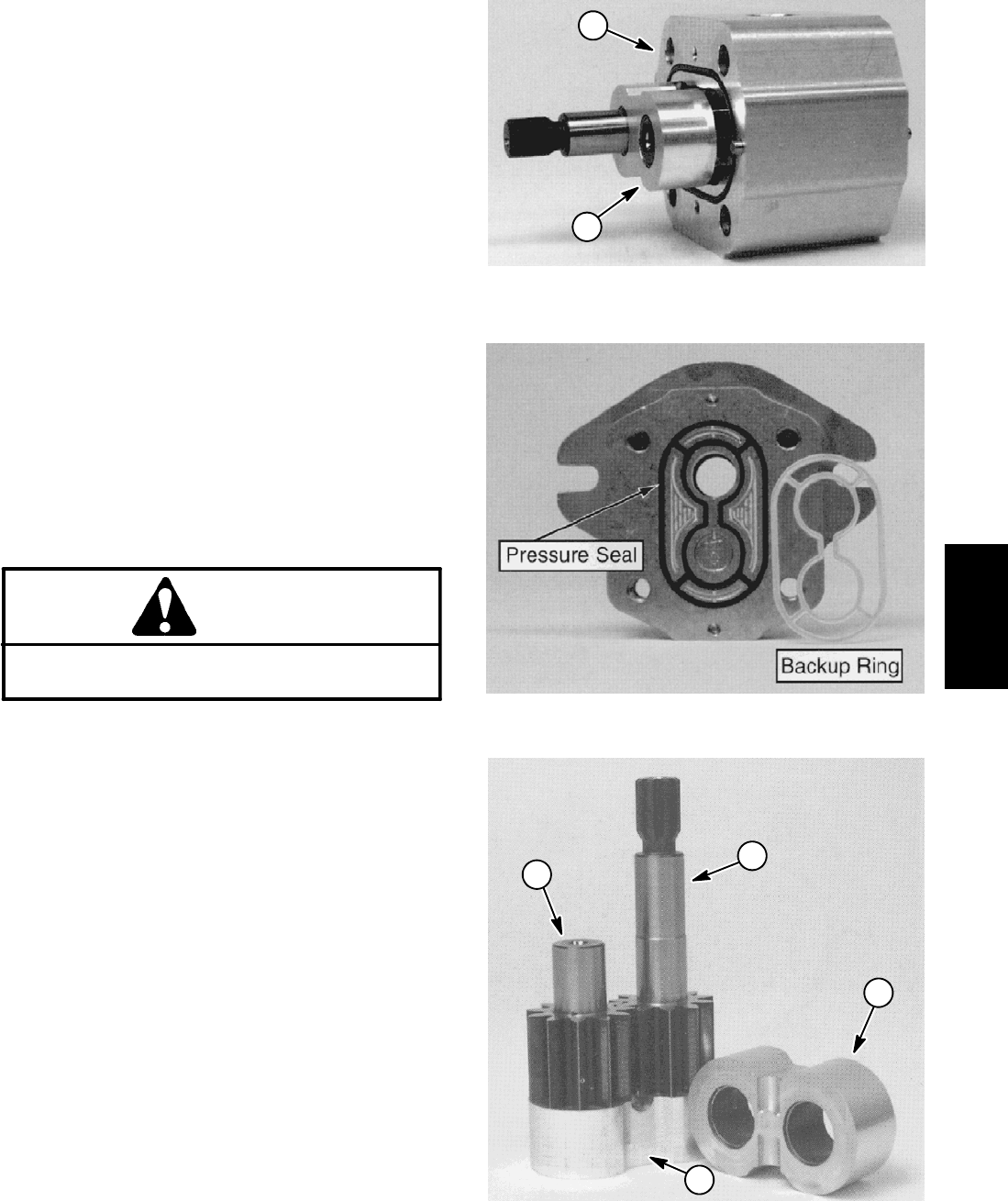
Groundsmaster 4000--D/4010--D Hydraulic SystemPage 4 -- 131
IMPORTANT: Mark the relative positions of the gear
teeth and the bearing blocks so they can be re-
assembled in the same position. Do not touch the
gearsurfacesasresidueon handsmay becorrosive
to gear finish.
7. Placethemotoron its side and push ontherearbear-
ing block to remove the bearing block and gear set (Fig.
103).
8. Carefully remove and discard O--rings, pressure
seals and back--up rings (Fig. 104) from motor. Do not
cause any damage to the machined grooves during the
removal process.
IMPORTANT: Make sure not to damage the counter
bore when removing the shaft seal from the front
plate.
9. Position front flange with seal side up. Carefully re-
move shaft seal taking care to not damage seal bore.
Inspection
1. Remove any nicks and burrs from all motor compo-
nents with emery cloth.
CAUTION
Use eye protection such as goggles when using
compressed air.
2. Clean all motor components w ith solvent. Dry all
parts with compressed air.
3. Inspect drive gear, idler gear and bearing blocks
(Fig. 105) for the following:
A. Gear shafts should be free of rough surfaces and
excessive wear at bushing points and sealing areas.
Scoring, rough surfaces or wear on gear shafts indi-
cates need for replacement.
B. Gear teeth should be free of excessive scoring
and wear. Any broken or nicked gear teeth must be
replaced.
C. Inspect gear face edge for sharpness. Sharp
edges of gears will mill into bearing blocks and, thus,
must be replaced.
D. Bearing areas of bearing blocks should not have
excessive wear or scoring.
E. Face of bearing blocks that are in contact with
gears should be free of wear, roughness or scoring.
4. Inspect front flange, body and rear cover for damage
or wear.
1. Motor body 2. Bearing block & gear set
Figure 103
1
2
Figure 104
1. Drive gear
2. Idler gear
3. Bearing block
Figure 105
1
2
3
3
Hydraulic
System