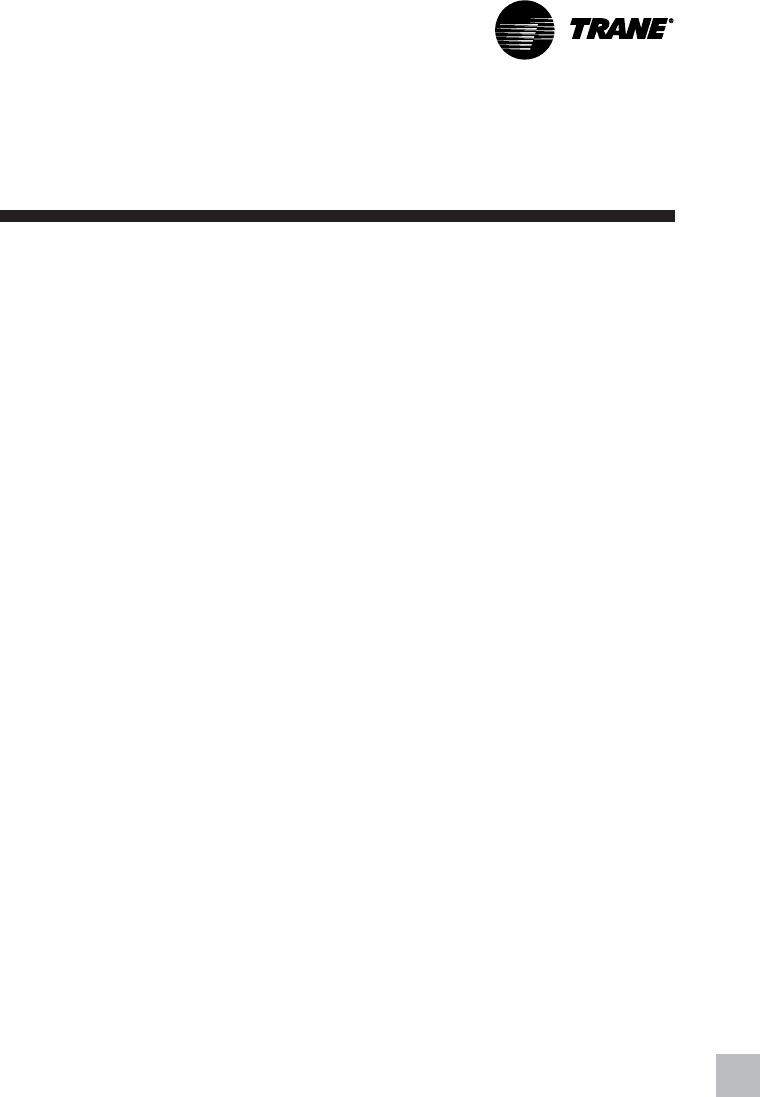
41
ABS-PRC001-EN
Mechanical
Specifications
Adaptive Limits
• Evaporator-water temperature limit
• Low absorber/condenser limit
• Soft-loading control
System Protection
• Evaporator freeze protection
• Chilled-water flow confirmation
• Cooling-water flow confirmation
• Emergency stop/shutdown
• Under/over voltage detection
Monitor and Displays
• Chilled-water temperature entering and
leaving
• Absorber/condenser water temperature
entering and leaving
• Solution concentrations
• Solution temperatures
• Total pump current
• Unit voltage
• Chiller run-time and starts
• Purge operation and run time
• Alarm light
• Diagnostic messages
• Help screens
• Evaporator-water flow (option)
• Cooling-water flow (option)
Interfaces To UCP2
™
• External machine manual-reset alarm
indication output
• External machine auto-reset warning
indication output
• External limit warning-indication output
• Maximum capacity indication output
• External auto-stop/emergency
shutdown
• Interface to Tracer Summit
™
• External chilled-water setpoint
• Tracer
™
controlled relay
• Printer interface
Contractor Responsibilities
1. Install the unit on a level surface.
Neoprene isolation pads supplied by
the manufacturer shall be placed
under the unit.
2. Connect the unit control panel to all
operating external safety and
auxiliary control devices.
3. Insure that piping adjacent to the
machine does not restrict removal of
headers for inspection, cleaning and
removing tubes.
4. Provide gauge cocks and optional
thermometer wells for temperature
and pressure readings at the inlet
and outlet of the evaporator, at the
inlet and outlet of the absorber, and
at the outlet of the condenser.
5. Provide balancing valves in all
external water circuits to allow
balance and trim of the system.
6. Provide and install strainers ahead of
all pumps and automatic modulating
valves to insure proper pump and
valve operation.
7. Insulate the chilled-water headers
and other portions of the unit, as
pointed out in the manufacturer’s
installation literature, to prevent
condensation on cold surfaces.
8. Provide and install a flow switch in
the chilled-water circuit, and interlock
it with the starting control circuit of
the unit. Proof of flow is required
prior to permitting unit operation.
Provide and install a flow switch in
the tower-water circuit, which shall
be interlocked with the starting
control circuit of the unit such that
proof of flow is required to prevent
machine damage
9. Provide necessary distilled or
demineralized water for refrigerant
charge and trim charge.
10. Provide labor to charge the machine
with lithium bromide solution and
refrigerant water, and assist in
machine starting and calibration
under supervision of the
manufacturer’s representative.
11. Provide an appropriately-sized
vacuum pump and personnel to
evacuate the unit prior to charging (if
required).
12. Field assemble machines (if required)
and leak test in accordance with
instructions in the manufacturer’s
installation bulletin.
13. Connect the rupture disc to an
appropriate floor drain or retention
chamber. The vent piping shall be
supported and connected by a
flexible connector to prevent stress at
the connection.
14. Install any control components
provided by the manufacturer for
installation external to the machine.
15. Furnish and install, external to the
unit control panel, a separately-fused
disconnect switch, if not provided.
16. Install required power supply wiring
to the control panel. Use copper wire
only.
Insulation Required
Insulation is required on cold areas to
prevent sweating. Insulation is available
as a factory provided, factory installed
option.
Insulation for cold insulation area should
be ¾-inch [19 mm] Armaflex or
equivalent, and should be applied to
evaporator waterboxes, refrigerant
storage tank, refrigerant pump and
refrigerant piping.
Cold insulation area on ABSD requires
__________ per unit.
Cold insulation area for pipes on
requires __________ linear ft. of pipe
insulation.