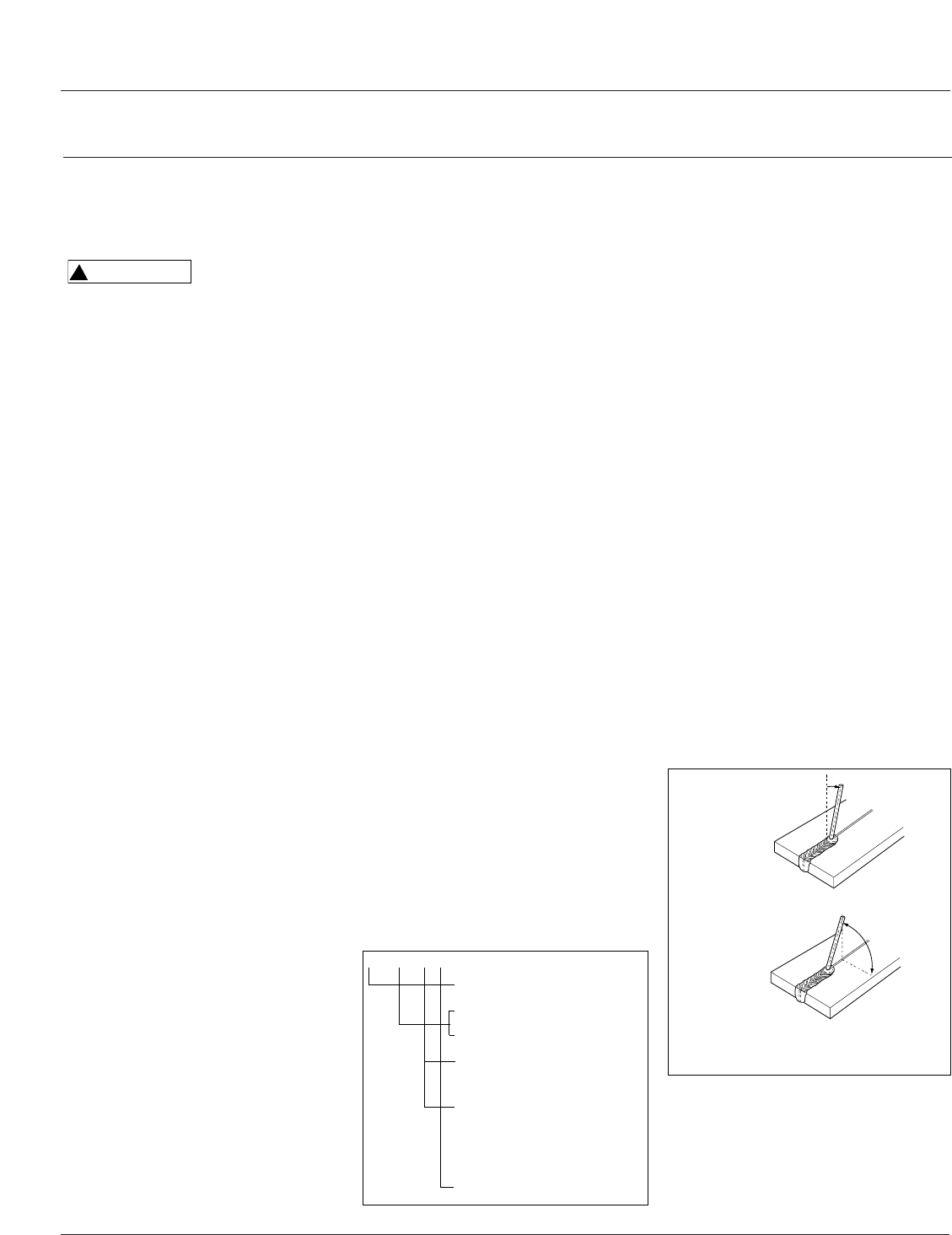
6
Operating Instructions and Parts Manual
www.chpower.com
Inverter Technology Arc Welder
reduce tiring of the hand and arm.
Note: Always keep the jaws of the
holder clean to insure good electrical
contact with the electrode.
Be careful not to
touch the work
piece or welding bench with the
electrode as this causes arc flashes.
There are two methods which can be
used to start or strike the arc; the
tapping method and the scratching
method. In the tapping method, the
electrode is brought straight down and
tapped on the work piece.
With the scratching method, drag the
electrode at an angle along the surface
much like striking a match. Regardless
of method, upon contact with the
plate, immediately raise the electrode
a distance equal to the diameter of the
electrode or it will stick to the surface.
Always hold the electrode pointed into
the weld.
Note: Should the electrode stick to the
work piece, break it loose by quickly
twisting or bending at the holder while
pulling upward. If the electrode does
not break loose, disengage the
electrode by releasing it from the
holder.
Arc Welding Basics
Five basic techniques affect weld
quality. These are: electrode selection,
current setting, weld angle, arc length,
and travel speed. Proper implementation
of these techniques is necessary for
good weld quality.
Electrode Type and Size
The correct choice of electrode type
involves a variety of factors, such as
welding position, work piece material
type, thickness, and condition of
surface to be welded. The American
Welding Society, AWS, has set up
certain requirements for each type of
electrode.
All electrodes are classified into five
main groups: mild steel, high-carbon
steel, special alloy steel, cast iron, and
nonferrous such as aluminum. The
majority of arc welding is done with
the electrodes in the mild steel group.
!
WARNING
The electrode material should corres-
pond with the work piece material.
Flux coatings are made for use with
either AC (alternating current), DC
(direct current) reverse polarity, or DC
straight polarity, although some
function well on both AC and DC
current.
Commonly Used Electrodes
1. E-6011 Deep Penetrating
• The strong arc force and rapid
solidification of the metal makes
vertical and overhead welding
easier with this rod.
• Where time does not permit rust,
scale or paint removal, this rod
penetrates rapidly and easily.
• Acceptable for AC or DC welding
current (reverse polarity).
2. E-6013 General Purpose
• All position, smooth deposit rod
with low spatter.
• For all mild steel and general
purpose work.
• Acceptable for AC or DC welding
current (straight or reverse
polarity).
3. E-7014 Iron Powder
•A general purpose "drag" rod for
all positions.
• Ideal for situations where fit
between metal pieces is poor.
• The iron powder in the flux coating
combines with the filler rod to
make a smooth deposit with very
little spatter.
• Ideal for ornamental work.
• Acceptable for AC or DC welding
current (straight or reverse
polarity).
4. E-7018 Low Hydrogen
• An all position high strength
electrode designed to produce low
hydrogen content combined with
excellent mechanical properties.
• Acceptable for AC or DC welding
current (reverse polarity).
Current
The correct current involves the
adjustment of the welding machine to
the required amperage setting. Current
represents the actual flow of electricity
and is regulated by a knob on the
welder. The current used depends on
the size (diameter) and type of
electrode used, position of the weld,
and the thickness of the work piece.
Consult specifications listed on the
electrode package or generalized chart
in the Operation section. Excessive
current burns through light metals,
and the weld bead is flat and porous or
the bead undercuts the work piece
(See Fig. 11). The bead appears high
and irregular if the current is too low.
Weld Angle
Weld angle is the angle at which the
electrode is held during the welding
process. Using the correct angle
ensures proper penetration and bead
formation. As different welding
Travel Angle
Work Angle
5º - 45º
E - 6 0 1 3
E=Electrode
60= Mild steel
70= High strength Steel
1=Electrode can be used
in all positions
2=Electrode is restricted
for use in flat or
horizontal position
only
Flux type
AWS Electrode Classification
Figure 8 - Weld Angle