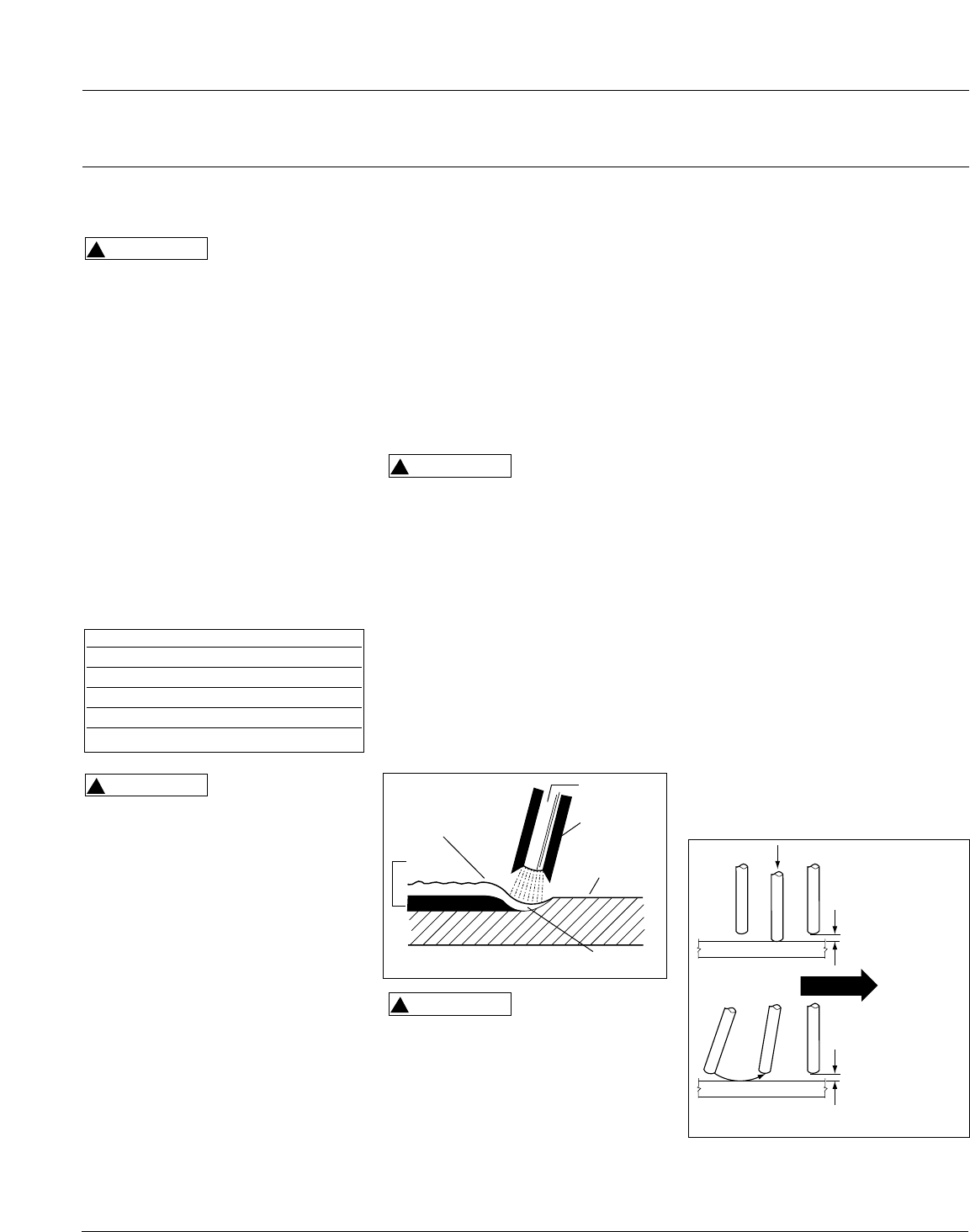
actual weld time that can occur in a ten
minute interval. For example, at a 10%
duty cycle, actual welding can occur for
one minute, then the welder must cool
for nine minutes.
Internal components of this welder are
protected from overheating with an
automatic thermal switch. A yellow
lamp is illuminated on the control panel
if the duty cycle is exceeded. Welding
operations may continue when the
yellow lamp is no longer illuminated.
Maintenance
Disconnect power
supply and turn
machine off before inspecting or
servicing any components.
Before every use:
1. Check condition of weld cables and
immediately repair or replace any
cables with damaged insulation.
2. Check condition of power cord and
immediately repair or replace any
cord if damaged.
3. Check condition of electrode holder
insulating pieces and immediately
replace cracked or missing insulators.
Verify that all fasteners are tight and
insulated.
Do not operate this
welding machine
with cracked or missing insulation on
welding cables, electrode holder, or
power cord.
Every 3 months:
Replace any unreadable labels on the
welder. Use compressed air to blow all
dust and lint from the ventilation
openings.
!
WARNING
!
WARNING
Model WS2100
5
protection with proper shade, flame
resistant clothing, leather welding
gloves, and full foot protection.
If heating,
welding, or cutting
materials that are galvanized, zinc
plated, lead, or cadmium plated refer
to the General Safety Information
Section for instructions. Extremely
toxic fumes are created when these
metals are heated.
4. Connect the ground clamp to the
work piece or workbench (if metal).
Make sure the contact is secure, and
not obstructed by paint, varnish,
corrosion, or non-metallic materials.
5. Insert the exposed part of the
electrode (the end with no flux) into
the jaws of the electrode holder.
6. Set the amperage adjustment knob
to the proper amperage for the
electrode diameter. Refer to the
following chart for proper electrode
current settings.
The electrode
holder and rod are
electrically "hot"(have current
potential) when the welder is on.
Grounding against any metallic surface
may produce an arc which could cause
sparks and damage eyesight.
7. Hold the electrode and holder away
from the grounded work piece or
workbench. Turn on the welder. A
green light is illuminated when the
welder power is on.
8. Position the electrode to begin weld,
lower the welding helmet or position
the hand shield, and strike an arc.
Adjust weld amperage as needed.
9. When finished welding, turn welder
off and store properly.
Duty Cycle / Thermostatic
Protection
Welder duty cycle is the percentage of
!
WARNING
!
WARNING
Welding Guidelines
General
This line of welding machines utilizes a
process known as Shielded Metal-Arc
Welding (SMAW). This process is used
to bond metals by heating them with
an electric arc created between the
electrode and the work piece.
Electrodes used for shielded metal arc
welding have two parts. The inner core
is a metal rod or wire that should be
similar in composition to the base
metal. The outer coating is called flux.
Various types of flux exist. Each coating
is used for a particular welding
situation.
While the metal is molten, it can be
contaminated by elements in the air.
This contamination could weaken the
weld. The flux coating creates a
protective barrier called slag that
protects the molten metal from
contaminants.
When current (amperage) flows
through the circuit to the electrode, an
arc is formed between the end of the
electrode and the work piece. The arc
melts the electrode and the work piece.
The melted metal of the electrode
flows into the molten crater and forms
a bond with the work piece as shown.
Note: Discontinue using and discard
electrodes that burn down to 1 to 2
inches from the electrode holder.
Striking an Arc
Place the bare end of the electrode in
the holder. Grip the holder lightly to
www.chpower.com
Amperage Output Guide
Electrode Diameter Current Setting
1/16” 30-60 Amps
5/64” 40-70 Amps
3/32” 60-100 Amps
1/8” 90-110 Amps
Slag
Weld
Wire
Flux
Work piece
Crater
Figure 6 - Weld Components
Same as
electrode
diameter
Same as
electrode
diameter
Figure 7 - Striking An Arc