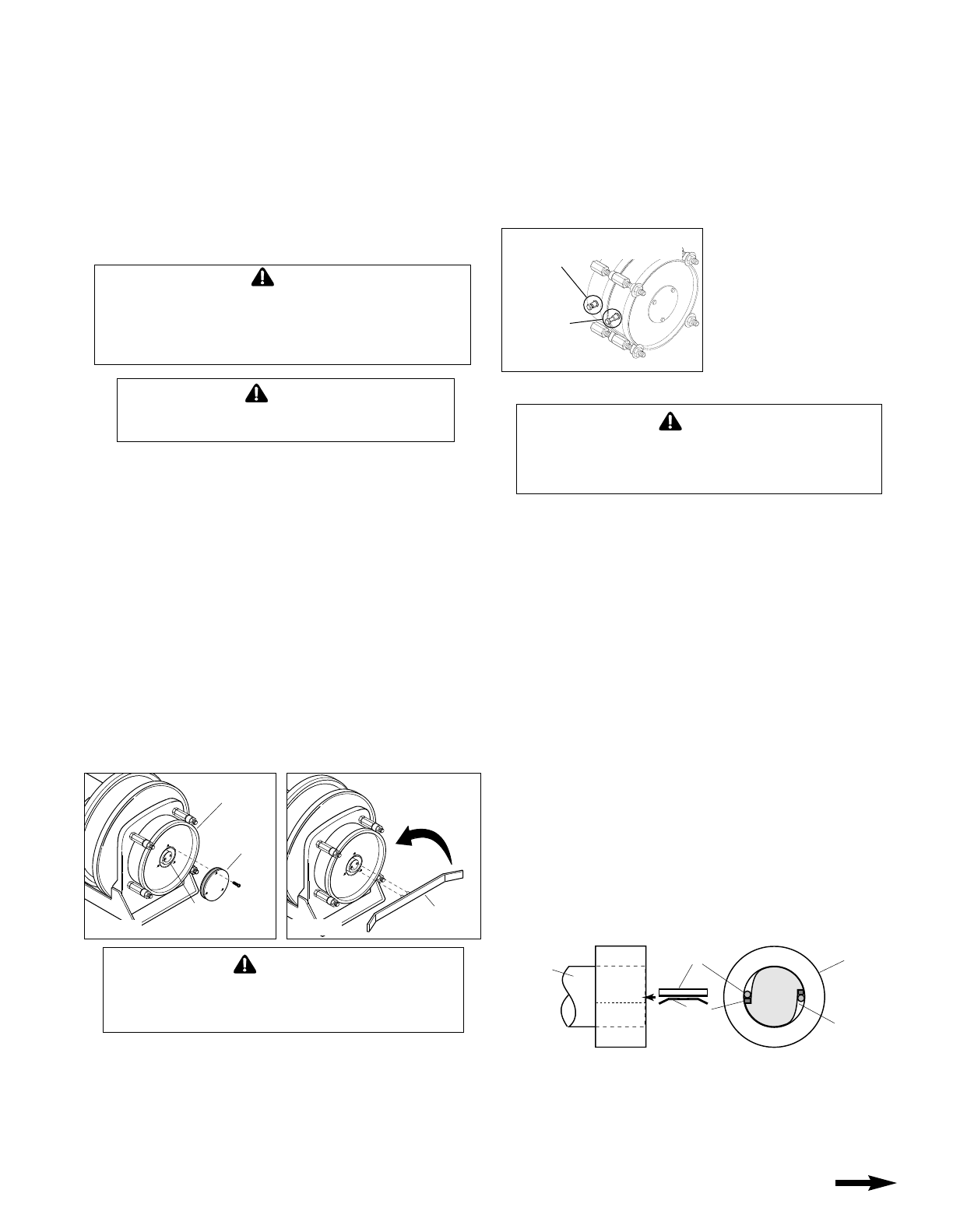
CONTINUED ON BACK PAGE
INSTALLATION and MAINTENANCE INSTRUCTIONS
UE21 UNIVERSAL CABLE REEL-DIRECT DRIVE
Printed in USA Bulletin No. 045393.a
®
HUBBELL
®
A Hubbell Company
GLEASON REEL CORP.
P.O. Box 26 • 600 South Clark St.
Mayville, WI 53050–0026
Phone 920–387–4120 • Fax 920–387–4189
All units are provided with right hand rotation unless otherwise
specified. This means that cable is pulled off spool top left or
bottom right (spool rotates clockwise to wind cable) when
viewing spring end of reel. See diagram on parts page.
Clock-type springs provide power for automatic cable take-up.
Spring must be pretensioned at time of installation to
insure that tension is applied to cable at all times. A tension
adjustment spanner wrench is provided with each reel.
INSTALLATION
1. Insure that machinery to be serviced by reel is at position
closest to reel.
2. Securely mount reel in desired position using 1/2"(M12)
bolts. Be sure spool is aligned with cable run.
3. Position optional cable guide, if reel is so equipped.
See COMPONENT REFERENCE DRAWING.
4. Connect free end of cable to junction box on machine or
adjust cable stop so that desired length of cable
extends from reel.
5. Remove cover plate on spring housing to expose
shaft and spring hub. (See Figure 1).
6. Insert spanner wrench into holes in spring hub (Fig 2).
Rotate wrench counterclockwise (for standard rotation).
Number of 360
O
turns should match last digit in model
number on serial plate.
If model number includes an “R”,
reel is reverse rotation and wrench must be rotated
clockwise.
(See “TO DETERMINE ROTATION OF REEL”
on parts drawing page.)
NOTE: If reel is equipped with ratcheted adjustment
wrench, follow instructions on separate sheet.
NOTE: On reels containing more than one spring, the hubs
are connected at the factory. Therefore, by tightening the
outer spring, the inside spring(s) will be tightened.
7. Remove collector cover and connect individual supply
conductors to collector terminals. See ELECTRICAL
CONNECTIONS diagram, on back page.
Do not attempt to relieve spring tension using span-
ner wrench. Doing so may result in personal injury.
WARNING
Some reels with large or multiple springs are equipped with
a ratcheted adjustment wrench. Follow separate instruc-
tions for its use. Failure to use ratcheted wrench, on reels
so equipped, could result in serious personal injury.
WARNING
Do not exceed number of turns indicated on
serial plate. Over-tensioning can cause a
broken spring, sheared shaft or other damage.
CAUTION
COVER
PLATE
SPRING
HUB
SPRING
HOUSING
COUNTER-
CLOCKWISE
FOR STANDARD
ROTATION
SPANNER
WRENCH
Figure 1
Figure 2
MAINTENANCE
Periodically: A. Use compressed air to clean collector
assembly and inside of collector housing. Inspect collector
assembly for brush wear and pitted slip rings.
B. Inspect cable for wear and check mounting bolts and
other hardware for tightness.
C. Check for broken
springs by pulling about 2/3
cable off reel and observing
“Broken Spring Indicators” on
sides of spring canisters. See
Fig. 3.
NOTE: Bearings and springs
are prelubricated and require
no periodic maintenance.
SPRING REPLACEMENT
The unique SAFETYCHANGE® spring motor consists of a
spring and hub sealed within a housing. A replacement spring
is supplied sealed in its housing and the old unit should be dis-
carded completely.
1. Turn off all electric power.
2. Disconnect cable from machine junction box.
3. Wind all cable onto reel to relieve all spring tension.
4. Remove inspection cover from face of spring housing.
5. Rotate spool clockwise and observe inner shaft. Shaft
should rotate clockwise and hub (with spring attached)
should remain stationary.
NOTE: Do not attempt to remove spring if resistance
is met or hub tends to rotate with shaft.
Continue to rotate spool and strike end of shaft
several sharp blows with a lead hammer or rubber mallet
until shaft rotates freely and hub remains stationary.
6. Remove (4) nuts which secure spring motor(s) to frame.
7. Slide spring motor(s) off shaft and discard.
NOTE: On multi-spring reels, be sure to remove and save
dowel pins which connect one spring hub with another. Also
remove snap rings on shaft between reel housings.
8. Install replacement spring motor(s), pawls and pawl springs.
NOTE: Pawl springs must be located between the pawls
and the deepest section of the shaft grooves. Make sure
that pawls and pawl springs are inserted flush with ends of
shaft and hub or they may rub against inspection cover.
9. Tighten nuts (and extension bolts) securing spring
housing(s) to reel frame.
10. Connect free end of cable to junction box on machine or
adjust cord stop so that desired length of cord extends from reel.
11. Tension spring with spanner wrench. Refer to
INSTALLATION section.
12. Replace inspection cover.
Do not attempt to remove spring from its housing. Clock-
type springs can be dangerous to handle. Removal of
spring from housing could result in personal injury.
WARNING
BROKEN SPRING
INDICATORS
“IN” with 2/3
cable off reel–
SPRING OK
“OUT” with 2/3
cable off reel–
SPRING
BROKEN
Figure 3
PAWL
SIDE VIEW
END VIEW
SPRING
Install
against flat
SPRING
HUB
(Spring not
shown)
SHAFT
GROOVE
SPOOL
SHAFT
CABLE REMOVAL
Use the following procedure to remove worn or damaged cable
from reel prior to installation of new cable.
1. Move machine serviced by reel to a position closest to
reel. Springs will still be under pre-tension at this point.
2. Turn off all electric power.
3. Lock spool to prevent turning using either a spool lock
mechanism or by tying off.
4. Disconnect cable from machine junction box.
5. Grip spool by hand and carefully release spool lock or
tie. Slowly unwind remaining tension.
6. Again lock or tie spool to prevent rotation.
7. Remove cable from spool. Loosen cable clamp and
water-tight connector. Disconnect conductors from slip ring
and remove cable.
8. Install new cable following instruction at right.
CABLE INSTALLATION
Use the following procedure to replace cable or if reel was
ordered without cable. Refer to ELECTRICAL CONNECTIONS
DRAWING, below.
1. Unspool new cable from shipping spool and lay out
to eliminate twist.
NOTE: This step is not essential, but will aid in winding
operation of the reel and prolong cable life.
2. Feed one end of the cable through water-tight connector on
the spool hub inside the spool and into the slip ring.
(See drawing below).
NOTE: This may require that jacket of cable be stripped
to allow conductors to pass through shaft.
3. Connect individual conductors to appropriate rings on
collector using crimp fitting or similar connection method.
4. Tighten water-tight connector. Place cable clamp on cable
and securely fasten to spool disk.
5. Wind the cable onto the reel spool by hand rotating
spool in direction it turns free of spring tension.
6. Connect free end of cable to machine junction box.
7. Pretension reel and complete installation as
previously described.
COLLECTOR REPLACEMENT
1. Turn off all power to reel.
2. Remove collector cover and gasket.
3. Disconnect electric leads to and from collector.
4. Remove button plug from hole in side of housing. Insert
long 1/8” Allen wrench through hole and loosen two set
screws in collector locking collar Set screws are at 90
O
to one another..
5. Slide collector off shaft.
6. Install new collector by reversing above steps.
Failure to relieve all spring tension prior to removing
cable could result in damage to equipment or personal
injury. Follow instructions carefully.
CAUTION
ELECTRICAL CONNECTIONS
SLIP-RING LEAD TO
MOVING CABLE
CONNECTIONS
SLIP-RING
LEADWIRES ARE
NUMBER TAGGED
LEADWIRE INPUT FIXED END
(CUSTOMER SUPPLIED)
CABLE LEADWIRES
MOVING END
CABLE
CABLE
CLAMP
SET
SCREW
COLLAR
WATER–TIGHT
CABLE CONNECTOR
BRUSH TERMINAL
CONNECTIONS
SLIP–RINGS
SPOOL
DISK
SPOOL
HUB
432
1
4321
FRAME
SLIP–RING ENCLOSURE
•
600 VOLTAC. 250 VOLT DC. WATERTIGHT, DUSTTIGHT.
•
DO NOT EXCEED AMPERAGE RATING OF CABLE OR SLIP RING.
•
NUMBER OF CIRCUITS MAY VARY FROM TWO (MINIMUM) TO 36 (MAXIMUM). FOUR CIRCUITS SHOWN.
NOTE:
Wire size, wire connectors, connection sequence,
and connection methods must comply with
National Electrical code and Local Electrical ordi-
nances. If in doubt, contact a local electrical con-
tractor or electrical inspector.
COLOR SEQUENCE FOR TYPE SO CABLE
THREE CONDUCTOR CABLE
# 1 – BLACK
# 2 – WHITE
# 3 – GREEN (ground)
FOUR THRU TWELVE CONDUCTOR CABLE
# 1 – BLACK
# 2 – WHITE
# 3 – RED
# 4 – GREEN (ground)
# 5 – ORANGE
# 6 – BLUE
# 7 – WHITE W/ BLACK TRACER
# 8 – RED W/ BLACK TRACER
# 9 – GREEN W/ BLACK TRACER
#10 – ORANGE W/ BLACK TRACER
#11 – BLUE W/ BLACK TRACER
#12 – BLACK W/ WHITE TRACER